Professional Advice on What is Porosity in Welding and Exactly How to Resolve It
Professional Advice on What is Porosity in Welding and Exactly How to Resolve It
Blog Article
Porosity in Welding: Identifying Common Issues and Implementing Finest Practices for Prevention
Porosity in welding is a prevalent concern that often goes undetected till it triggers substantial troubles with the integrity of welds. This usual defect can jeopardize the stamina and longevity of welded frameworks, presenting security dangers and resulting in costly rework. By comprehending the root causes of porosity and implementing effective prevention strategies, welders can dramatically boost the high quality and reliability of their welds. In this discussion, we will certainly explore the crucial factors adding to porosity formation, analyze its damaging effects on weld efficiency, and talk about the best techniques that can be embraced to minimize porosity event in welding processes.
Usual Sources Of Porosity

Utilizing filthy or wet filler products can present impurities right into the weld, contributing to porosity concerns. To minimize these usual causes of porosity, detailed cleaning of base metals, proper shielding gas choice, and adherence to ideal welding specifications are essential practices in achieving high-quality, porosity-free welds.
Influence of Porosity on Weld Top Quality

The presence of porosity in welding can considerably jeopardize the structural honesty and mechanical residential properties of welded joints. Porosity produces voids within the weld steel, deteriorating its total toughness and load-bearing capability. These voids work as stress and anxiety concentration factors, making the weld more prone to cracking and failure under used tons. Additionally, porosity can decrease the weld's resistance to deterioration and other ecological elements, better decreasing its long life and efficiency.
Among the key consequences of porosity is a decline in the weld's ductility and sturdiness. Welds with high porosity levels often tend to display lower effect strength and reduced capability to flaw plastically prior to fracturing. This can be especially concerning in applications where the welded parts undergo vibrant or cyclic loading problems. Furthermore, porosity can hamper the weld's capacity to effectively transfer pressures, leading to premature weld failing and prospective safety and security threats in crucial frameworks.
Finest Practices for Porosity Prevention
To improve the architectural stability and top quality of bonded joints, what certain actions can be applied to reduce the incident of porosity throughout the welding process? Porosity avoidance in welding is vital to make certain the honesty and stamina of the last weld. One effective method appertains cleaning of the base metal, removing any pollutants such as corrosion, oil, paint, or wetness that could cause gas entrapment. Making certain that the welding tools is in good condition, with clean consumables and ideal gas circulation prices, can likewise considerably reduce porosity. In addition, preserving a secure arc and regulating the welding criteria, such as voltage, current, and take you could try here a trip speed, assists develop a regular weld pool that reduces the risk of gas entrapment. Utilizing the appropriate welding method for the particular product being bonded, such as adjusting the welding angle and weapon position, can further avoid porosity. Normal assessment of welds and instant removal of any type of concerns identified throughout the welding procedure are necessary techniques to avoid porosity and create premium welds.
Importance of Appropriate Welding Strategies
Executing appropriate welding techniques is vital in ensuring the architectural integrity and quality of bonded joints, developing upon the structure of reliable porosity prevention measures. Welding strategies straight affect the general toughness and sturdiness of the bonded framework. One essential aspect of correct welding techniques is preserving the appropriate heat input. Extreme warm can bring about boosted porosity as a Home Page result of the entrapment of gases in the weld pool. Alternatively, insufficient heat might result in insufficient blend, developing potential weak points in the joint. Additionally, using the ideal welding specifications, such as voltage, existing, and take a trip speed, is essential for accomplishing audio welds with very little porosity.
Furthermore, the option of welding process, whether it be MIG, TIG, or stick welding, must line up with the certain requirements of the project to make certain optimum outcomes. Correct cleaning and prep work of the base metal, along with picking the ideal filler product, are likewise crucial components of efficient welding methods. By sticking to these finest methods, welders can minimize the danger of porosity formation and create top notch, structurally sound welds.
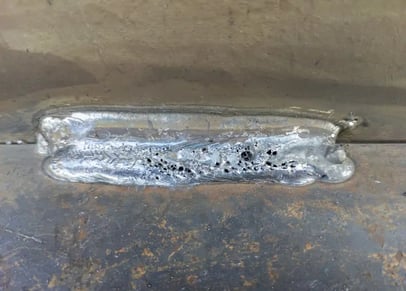
Testing and Quality Control Measures
Quality control procedures play an essential duty in validating the honesty and integrity of bonded joints. Checking treatments are necessary to detect and prevent porosity in welding, making certain the strength and toughness of the end product. Non-destructive screening methods such as ultrasonic testing, radiographic screening, and aesthetic assessment are frequently used to identify potential issues like porosity. These strategies allow for the assessment of weld top quality without endangering the integrity of the joint. What is Porosity.
Post-weld assessments, on the various other hand, assess the final weld for any issues, consisting of porosity, and confirm that it satisfies specified requirements. Applying a detailed high quality control plan that consists of detailed testing treatments and assessments is extremely important to lowering porosity issues and ensuring the total quality of bonded joints.
Final Thought
To conclude, porosity in welding can be an usual problem that influences the quality Resources of welds. By recognizing the usual reasons for porosity and executing finest methods for avoidance, such as proper welding techniques and testing procedures, welders can guarantee high top quality and reliable welds. It is important to prioritize avoidance methods to reduce the incident of porosity and keep the integrity of welded structures.
Report this page